撰文:鍾子葳日期:2020-09-14
從事紡織製造產業超過一甲子的東豐纖維,因應數位時代的浪潮,和工研院合作,轉型為智慧工廠,透過無人搬運車、自動驗布機和雲端智慧生產等方式,大幅提升了生產效率,也為公司帶來極大的經濟效益。
「答答答答…」寬廣的工廠裡充斥著機械聲,四百多台織布機正忙碌地工作著,一眼望去,除了一輛穿梭在廠房裡的無人搬運車之外,幾乎看不見人影。
這是東豐纖維位在高雄路竹的染整廠,有9成以上的產量,專為adidas、Nike、PUMA等世界知名的運動品牌製作衣服,「Levi’s、Calvin Klein、Dolce & Gabbana(DG)等知名服飾品牌也是我們的客戶。」東豐纖維總經理陳裕隆笑著說道。
但是,這樣一間在全球有14間成衣廠、2間織布染整廠的大公司,卻曾面臨被時代淘汰的危機。
2014年,東豐纖維路竹廠正在慶祝六十周年的同時,這間老工廠也正面臨機器設備老舊、員工平均年齡偏高的困境。「客戶對於品質、速度和效率的要求愈來愈嚴格,因此我們覺得需要做一些改變。」陳裕隆總經理說道。
2015年,東豐纖維決定加碼投資,開啟轉型之路,除了與台灣產業服務基金會合作,通過工業局清潔生產的認證,並與工業技術研究院合作,引進雲端技術,將所有的生產數據連上網路,進一步發展工廠的自動化與智能化。
「其實在轉型的過程中,對於我們這樣一個傳統的產業及傳產從業人員來說,相較於高科技行業,我們缺少了數位DNA…」東豐纖維總經理陳裕隆說道。為了彌補這部分的缺陷,東豐纖維將「幹部年輕化」視為首要目標,陳裕隆總經理也感謝地表示,工研院除了幫助東豐克服技術上的難題以外,也帶動了中階幹部的成長。
為了減少人力,東豐纖維在2016年引進了TAIS自動驗布系統,「這家公司原本是以色列的軍火商,他們將頭盔上的影像技術運用在紡織業,藉由9台相機,每分鐘拍上千張的影像,可以精準地找出布料上的瑕疵。」陳裕隆總經理說道。
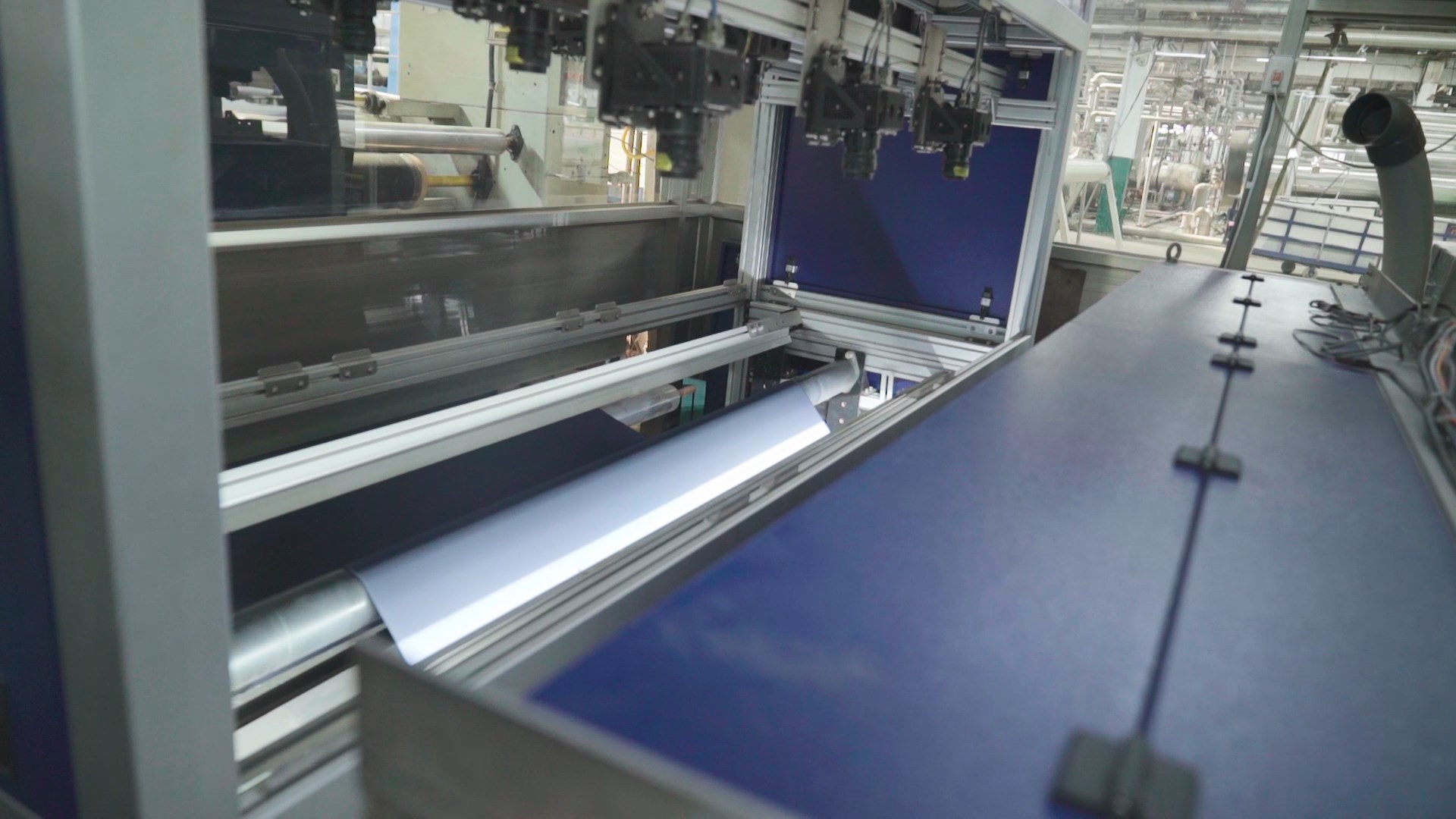
▲TAIS自動驗布系統透過鏡頭即可辨識出瑕疵,並可將資料直接傳給成衣廠,節省了不少驗布的時間。
他並舉例,過去驗一匹布料大約需要耗費40分鐘以上的時間,如今只需要用6分鐘的時間就能完成,準確率比過去人工檢驗多了50 %以上。再加上過去檢驗完的布料送到成衣廠之後,成衣廠又需要再抽檢15%的布料,又得再花上一段時間,現在可以直接透過網路,將資料傳送給成衣廠,大幅地減少驗布的時間,「這使得我們的交貨期可以從60天完成400萬碼,縮短至45天之內完成,甚至更短、更多數量。」陳裕隆總經理說道。
而除了升級驗布系統,東豐纖維也透過工研院的協助,研發AGV無人搬運車,讓織布機透過雲端智慧技術,建立機器之間的對話,「當織布機快完成作業時,會透過雲端系統通知我們的AGV過去搬貨,以前我們一個工人要自己扛布,400台的織布機等於要跑400 次,那真的非常地累!」陳裕隆總經理說道。
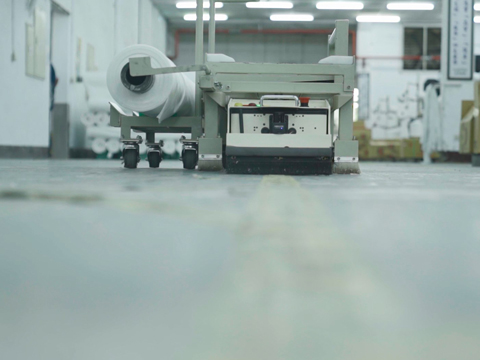
▲AGV無人搬運車可透過雲端智慧技術,自動到達完成織布工作的機台,搬運布料。
「東豐纖維不僅在生產上追求進步,我們也積極在推動綠色工廠。」陳裕隆總經理說道。東豐汰換掉老舊的設備,並使用耗能較少的機台,例如節能履帶式染色機,可節省30%的製程用水、50%加熱能源,縮練水洗機每月可節省432噸的用水。
「近幾年流行用回收寶特瓶做成衣,其實我們早在12年前就把這種布料推到美國市場了!在美國銷售第一名的西裝褲就是我們的布料做的,每年大概賣出兩百萬條褲子!」陳裕隆總經理驕傲地說道。
2018年,東豐纖維進一步成立創新研發中心,對外尋求產、官、學、研的合作夥伴,整合研發能量。陳裕隆總經理並表示,東豐纖維在過去一年持續地收集相關的生產數據,已累積上百萬筆的資料,未來將有助於公司在智慧生產的發展,「我們希望能夠盡量減少員工比較勞累和危險的工作內容,讓機器能夠自己對話、自己生產,讓員工投入在更重要的工作上,例如設計開發高附加價值的產品。」陳裕隆總經理補充道。
而談到轉型對於公司帶來的效益,陳裕隆總經理也與我們分享,雖然公司在過去4年的轉型路上,在自動化與智能化的投資上花費不少,但獲利仍持續成長約40%,織布生產量也成長了30%以上。「目前我們在路竹廠的員工有343人、泰國廠約700人,明年目標減少30%的人力,基本上是將操作員的人力轉往設計開發上。」陳裕隆總經理說道。
轉型後的東豐纖維,不僅僅是受許多國際品牌青睞的布品供應商或是成衣製造商,也進一步成為客戶的開發設計夥伴,從代工走向品牌。東豐纖維透過數位化的方式,讓這個傳統老工廠翻身,不僅為公司帶來實質上的效益,而他們也證明了,台灣的紡織業仍有足夠的實力在國際上發光發熱。